Mining and milling of uranium and thorium (Sustainability Assessment)
This page refers to "Safety of NFCFs" and presents contains a short description of the main processes found in a facility for uranium and thorium mining and milling (or processing)
Mining and milling of uranium
The discussion of uranium mining and milling in this section is mostly focused on the processes developed to recover uranium concentrate as the main product from the ore deposits mining, i.e. from conventional resources. Substantial amounts of uranium can be produced from unconventional resources, e.g. as a by-product of mining copper, gold, phosphates or rare earth elements. Radiation hazards in the mining and processing of unconventional uranium resources will depend on the uranium concentration in the deposit and can differ essentially from traditional mining and milling techniques. Safety issues of uranium recovery from unconventional resources are not specifically considered in the current edition of the INPRO methodology manual, however it is expected that the INPRO requirements and criteria formulated in this report will be applicable to a certain extent to the uranium production part of the process.
Uranium extraction technology, right from ore exploration to the ultimate recovery of the product, has developed rapidly over the past several decades. Significant innovations in mining, milling and leaching processes as well as in the use of equipment have also been achieved. A comprehensive description of uranium extraction technology is provided in Refs[1][2][3]. Open pit mining, underground mining, and in-situ leaching are the processes adopted worldwide for extraction of uranium.
Rock mining of uranium
Underground mining is generally economically preferable when the ore is located at greater depths (> 200 m). It consists of the following steps: identification and delineation of ore body using radiation detectors, drilling, blasting by remote control process, loose dressing and support, stowing, tramming and mucking. Very often ‘cut and fill’ and ‘open stope’ methods of underground uranium mining are used. Following identification of the area with rich uranium, a shaft is sunk in the vicinity of the ore and cross cuts are driven horizontally to the ore at various levels at an interval of 100 to 150 metres. Tunnels known as ‘drifts’ are driven along the ore from the cross cuts and tunnels known as ‘raises’ are made up and down from level to level, to reach the ore body. The ‘stope’ is the workshop for the mine, where ore extraction continues. Mining requires a network of shafts, tunnels and chambers connecting with the surface and allowing movement of workers, machine and rock within the mine, and services such as water, electric power, fresh air, exhaust and compressed air, drains and pumps to collect seeping ground water, and a communication system. Entry of miners after blasting is normally delayed till the dust and fumes disperse with ventilation air to the permissible level.
Open pit mining is usually preferable for shallower orebodies since the productivity is higher, ore recovery is better in comparison to underground mining due to lower dilution, dewatering of the open pit is easier and mining conditions are safer. The disadvantages include large-scale excavation resulting in huge overburden of rock and soil, land degradation and a chance of environmental contamination.
Milling of uranium after rock mining
Milling consists of the following steps (see Fig. 1): Transferring the ore by conveyor belt, crushing, and (wet) grinding the ore into sand and silt. This is followed by processing that involves leaching mostly with sulphuric acid in the presence of pyrolusite as an oxidant in large containers, anion exchange separation of uranium and purification and concentration of uranyl sulphate product. Precipitation is then carried out to remove iron and other metal impurities and to recover uranium typically as ammonium diuranate (ADU) or in a peroxide form. Finally, U3O8 is produced by dewatering and roasting (calcining).
Uranium milling tailings management
The barren liquor from ion exchange in the milling facility generates acidic liquid waste (where acid has been used in the leaching process) which contains most of the radium and other radionuclides dissolved in the leaching process and traces of uranium not absorbed in the ion exchange step. The slurry form called tailings includes solid waste containing the un-dissolved uranium, radium and other radionuclides. When acidic, these tailings are mixed with lime for neutralization and may be sent to a hydro cyclone, where sand and slime get separated. The sand can go to the mine for backfilling and the slime to a tailings pond.
The milling waste is normally transferred from the milling facility to a tailings management facility where it consolidates and settles over a period of many years. The decanted liquid from the tailings is normally recycled whenever possible or sent to the effluent treatment plant for chemical treatment and activity removal to enable its discharge to the public domain according to the norms specified by the regulatory authority. Finally, these tailings have to be disposed of in above ground impoundments (usually with dams), open pits or underground mine voids.
The wastes produced in a (underground or open pit) mine and milling facility include, in addition to mill tailings, also waste rock and mineralized waste rock. They contain only low concentrations of radioactive material and toxic chemicals but are generated in large volumes compared to other nuclear facilities, and therefore need to be safely stored and disposed of in accordance with regulatory requirements[4].
In this manual the tailing facility is treated as an integral part of the mining and milling facility (and not as a separate waste management facility).
Overview of technologies, strategies, methods and problems related to long term management of uranium tailings are described in Ref[5].
In situ leaching uranium mines
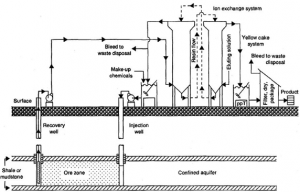
In situ leaching (ISL) mining is defined as the leaching of uranium from a host sandstone by chemical solutions and the recovery of uranium at the surface[1][2] (Fig. 2). ISL extraction is conducted by injecting a suitable leach solution into the ore zone below the water table; oxidizing, complexing, and mobilizing the uranium; recovering the pregnant solutions through production wells; and, finally, pumping the uranium bearing solution to the surface for further processing. ISL involves extracting the ore mineral from the deposit, with minimal disturbance of the existing natural conditions of the earth’s subsurface and surface.
Compared to underground and open pit mining, the in-situ leaching process does not introduce significant surface disturbance, eliminates the crushing, milling, grinding and leaching steps in the process, provides safer working conditions, does not generate large solid radioactive waste streams and requires less manpower. However, this process is applicable only for certain types of ores and detailed precautions are required to be taken to keep contamination from reaching water sources[2].
Thus, in contrast to underground and open pit mining, in the case of in-situ leaching (ISL) mines, there are no rock dumps and tailings storage facilities, no dewatering of aquifers, and much smaller volumes of mining and hydrometallurgical effluents that could contaminate the surface, air and water supply sources[6][2].
Safety issues in uranium mining and milling
Natural uranium consists of a mix of radioactive isotopes emitting some α-, β-, and γ-radiation. The level of γ-radiation from a lump of pure natural uranium is lower than from an equivalent sized lump of granite and gloves are normally considered as sufficient protection for handling metallic natural uranium[7]. However, the mining of uranium is always associated with its progenies such as radon and radium, which have much higher radiation hazards than uranium itself.
While radiation exposure is typically the potential human health hazard most associated with NESs, including their uranium mining and milling facilities, it is by far not the only hazard that humans are exposed to in such facilities. Uranium mining and milling involves most of the same hazards associated with other mining activities and the risks associated with radiation may not necessarily be the dominant contributors to the overall risk.
Ref[8] gives an overview of risk constituents in uranium mining, including those not related to radiation factors, such as the silica exposure that cannot be avoided during the rock mining and processing of uranium ore. Silica-caused adverse health outcomes are mostly respiratory disorders such as silicosis, which is characterized as “progressive, life-threatening, fibrotic lung disease”. Besides that, mining may involve traumatic injuries including fatal ones from explosions, fires, underground mine flooding, collapses of bulkheads, caving failures, rock falls, falls from height, entrapment, etc. Ref [78] provides data that can be used to estimate the rate of fatalities from traumatic injury in mining (including metal, nonmetal, stone, sand, and gravel mines) at about 20 per year per 100 000 full-time equivalent employees in the period from 1988 to 2007. Other non-radiation hazards in mining include electrical accidents, which “occur less frequently than other sources of traumatic injury, but they are disproportionately deadly” [78]; exposure to diesel fumes including carbon monoxide; nitrogen oxides in explosive gases; noise, vibration, etc.
Although normal industrial safety issues of uranium mining and milling, i.e. those not related to radiation exposure, have to be considered by the responsible national organisations as one of the most important parts of the authorisation process, these issues are deemed to be not directly linked to the sustainability of a NES and are not considered in the current edition of the INPRO methodology manual.
A large number of reports discuss the safety and environmental issues associated with uranium extraction activities[9][10][5][11][12][4][13][14][6][15][1][16][17][18][19][20]. The safety issues related to the ore extraction extend through the lifetime of mining and milling facilities including their decommissioning. Though these stages are different, the hazard potential remains more or less similar. The siting of uranium mining and related components needs to consider disposal of waste and final decommissioning without unduly affecting the environment (e.g. displacement of population, change in the land use, flora and fauna, etc.). Having selected a site through a detailed survey, an extensive baseline survey of the area is to be undertaken prior to actual operation. The study of baseline data consists of the existing environmental quality (air, water and land) in terms of existing pollution load (both conventional and radioactive), land use, socioeconomic status, land use pattern, flora and fauna. A change in any of the baseline values would serve as a performance indicator of the operation of mining and milling activities and could be used for safety and environmental assessment.
As discussed above in this section, the predominant occupational and environmental hazards of mining and milling of uranium may be no different from other mineral extraction processes. However, there are additional risks involved in uranium mining due to potential exposure to radioactive materials.
The major radiological safety issues in the entire process – mining, milling, leaching, product recovery, storage and disposal of tailings – are dust, chemical, and radiation exposure to the workers (and to the general public). The aspect of transport of ore or the product from site to site is yet another site-specific safety related issue. The three main sources of radiation exposure of mine workers are:
- Radioactive dusts that are breathed in;
- Gamma radiation from the ore that irradiates the body;
- Radon gas that is breathed in (in underground mines).
Open pit and underground mining and milling operations involving uranium have a potential to generate dust that contains radioactivity in varying quantities. The hazard potential is higher if the operations are dry and dusty rather than wet operations.
The progenies of natural uranium are in equilibrium with uranium and some of them, such as 214Bi and 214Pb, are strong gamma emitters that pose external exposure hazards. According to data provided by India, ca. 83 % of the gamma energy is emitted from 214Bi and 12 % from 214Pb. The individual dose from gamma radiation from an ore body of 0.5 % grade can reach 50 mSv/a. Similarly, the gaseous uranium progeny radon (222Rn) is another major source of radiation exposure to the workers in a mine and potentially also to workers in the milling and product extraction areas as well. Hence, safety in the design and operation of the process is of paramount importance and monitoring of workers’ dose in accordance with national regulatory requirements is essential.
Radiation exposures to the general public from normal operations and anticipated operational occurrences (AOOs) in the uranium ore processing industry needs to be less than 1 mSv in a year. The disposal of radioactive waste and the consequent dose from all pathways of exposure to the general public residing near the industry shall not exceed the quantities derived from the prescribed limits. The safety measures for the processing operations, transport, storage and disposal of the tailings, and for the ultimate decommissioning of the facility, shall result in exposures to the public well below the regulatory limits. The radiation exposure of the public and the environment caused by a mining and milling facility, including its tailings management facility, is covered in a separate manual of the INPRO methodology on the environmental impact by stressors.
Mining and milling of Thorium
Thorium mining is largely done by open-pit methods, dredging and beach sand collection.
Mineral sands mining and separation of thorium
The valuable minerals in mineral sands, such as ilmenite, rutile, sillimanite, garnet, zircon, monazite, etc, are mined and separated based on differences in physical properties. Thorium content in the sand is normally quite low[21]. Mining, separation and processing of these minerals involve operation of floating dredge or dry mining, gravity separation, application of high voltage and high magnetic fields, operation of dryers, and operation of material handling equipment like belt conveyors, bucket elevators, and mixer-settlers involving flammable materials.
Monazite is subjected to further processing to obtain thorium oxalate/thorium nitrate and ADU, whereas zircon frit powder can be obtained from zircon. Standard chemical processes involving digestion, solvent extraction, precipitation and filtration are used for this purpose. For example, processing of monazite, an orthophosphate of thorium and rare earth elements, is carried out by digestion of finely ground monazite with caustic soda, which results in three components, namely by-product tri-sodium phosphate, mixed hydroxides of rare earths, thorium and uranium as well as un-reacted monazite. After the majority of rare earths is first separated from the mixed hydroxide, the mixed hydroxides of thorium, uranium and residual rare earths are extracted through acid leaching. This is followed by solvent extraction to ultimately produce thorium oxalate and a crude uranyl chloride solution and to recycle the residual rare earths. The crude uranium chloride solution is subsequently refined to produce nuclear grade U3O8. As carried out in India[22], chemical processing of every ton of monazite containing ca. 9% of thorium to the thorium oxalate form produces approximately 0.08-0.10 ton of insolubles, 0.06-0.10 ton of Pb-Ba cakes and 0.1 ton of phosphates and other solid waste from effluent treatment. The solid wastes are buried in underground trenches. Liquid effluent is treated in the effluent treatment plant and then discharged after monitoring.
Safety issues in thorium mining
As the majority of thorium mining is by open-pit methods or by wet dredging, the radiological problems, particularly inhalation hazards, are relatively small compared to those in underground uranium mining. Inhalation hazards arise mainly from dust produced during the physical separation of the mineral constituents of placers or from thoron (220Rn) gas. The methods used in dry operations are magnetic and electrostatic separation, and separation by wind/air tables, which produce a lot of dust. Dust is also generated during drying and conveying, etc. Thorium is present in the dust during segregation of heavy minerals. Thus, the assessment of hazards needs to include, in addition to thoron, an assessment of thorium and its long-lived daughter products in the working atmosphere. The dose delivered to the lungs from breathing in an atmosphere containing thoron and its daughters arises principally from the decay of thoron and 216Po in the airways of the lung, and the deposition and subsequent decay of inhaled daughter products.
Most of the radiation exposures in the mineral sands industry come from the inhalation of airborne dust. However, if appropriate procedures are not followed, workers can also be exposed to external radiation. This external radiation may come from the emission of gamma radiation from final product storage or intermediate mineral stockpiles that have high monazite content. Most of the external radiation exposures in mineral sand processing plants can occur from being in close proximity to stored material. External radiation hazards arise from both beta and gamma radiation emitted by 228Ac (1 MeV gamma radiation, and 1.2, 1.7, 1.9 and 2.2 MeV beta radiation), 212Bi (2.25 MeV beta radiation) and 208Tl (1.8 MeV beta and 2.6 MeV gamma radiation).
Dust deposits on surfaces depend on the operational methods used and on the wetness of the mine; normally, it is not hazardous except possibly as a source of air contamination. However, clothing contamination may be a more significant source of exposure than in uranium mines because of the more pronounced beta and gamma emitters associated with thorium. Chemical processing of monazite to extract thorium involves grinding of monazite to reduce its particle size. This operation and subsequent handling of powdered monazite can lead to air borne dust. Thorium bearing monazite usually contains a very small amount of uranium, and although the typical ratio of thorium to uranium is 25:1, 222Rn and radon progenies may occur in significant air concentrations along with 220Rn and thorium in the initial chemical treatment areas of the plant.
Since the hazard from thoron is predominantly attributable to 212Pb, which occurs with thoron in all practical situations, it is permissible to apply the value for 212Pb as the standard of control for both radionuclides. Because of the very short half-lives of thoron 220Rn (55.6 s) and 216Po (0.15 s) compared to 212Pb (10.6 h), dilution ventilation is relatively ineffective for these radionuclides, but it can reduce the concentration of 212Pb by a large factor. Thus, in some atmospheres, the concentration of thoron may exceed that of 212Pb by orders of magnitude. This situation is restricted to places where clean ventilating air is continuously available at the source and therefore it could be manifested in mills. The dose from thoron itself may be comparable to that of 212Pb in cases of extreme non-equilibrium. External radiation is associated with the physical treatment of monazite. In the monazite stores and filling area, however, the radiation levels could be high.
The chemical treatment of monazite gives two fractions: the thorium fraction (consisting of 232Th and 228Th from the thorium series, and 234Th, 230Th, 231Th and 227Th from the uranium series) and the non-thorium fraction (consisting of 228Ra, 224Ra and other daughters from the thorium series, and 226Ra with daughters from the uranium series). The processing of monazite to extract thorium gives rise to generation of solid, liquid and gaseous wastes. The thorium ore monazite is essentially an orthophosphate of rare earths, thorium and uranium. As such, there is no significant problem of liquid waste in mining or in mineral separation plants using physical methods. However, the liquid effluents from the chemical processing of monazite contain the decay products from the uranium and thorium series. Because of suspended and total solid load in the effluents, they are allowed to pass through settling tanks, the clear overflow from which, after suitable dilution, can be released to nearby recipient water bodies.
See also
- NFCF
- Uranium refining/conversion and enrichment
- Uranium oxide and MOX fuel fabrication
- Reprocessing of spent nuclear fuel
- Storage of spent nuclear fuel
[ + ] Assessment Methodology | |||||
---|---|---|---|---|---|
|
References
- ↑ 1.0 1.1 1.2 1.3 INTERNATIONAL ATOMIC ENERGY AGENCY, Uranium Extraction Technology, IAEA Technical Report Series No. 359, IAEA, Vienna (1993).
- ↑ 2.0 2.1 2.2 2.3 INTERNATIONAL ATOMIC ENERGY AGENCY, In Situ Leach Uranium Mining: An Overview of Operations. IAEA Nuclear Energy Series No. NF-T-1.4, IAEA, Vienna (2016).
- ↑ WOODS, P. H., Uranium Mining (Open Cut and Underground) and Milling, Ch 6 In Hore-Lacy, I. (Ed.), Uranium for Nuclear Power: Resources, Mining and Transformation to Fuel. Woodhead Publishing, Cambridge, (2016).
- ↑ 4.0 4.1 INTERNATIONAL ATOMIC ENERGY AGENCY, Management of Radioactive Waste from the Mining and Milling of Ores, Safety Guide, IAEA Safety Standards Series No. WS-G-1.2, IAEA, Vienna (2002).
- ↑ 5.0 5.1 INTERNATIONAL ATOMIC ENERGY AGENCY, The Long Term Stabilization of Uranium Mill Tailings, IAEA-TECDOC-1403, IAEA, Vienna (2004).
- ↑ 6.0 6.1 INTERNATIONAL ATOMIC ENERGY AGENCY, Guidebook on Environmental Impact Assessment for In Situ Leach Mining Projects, IAEA-TECDOC-1428, IAEA, Vienna (2005).
- ↑ WORLD NUCLEAR ASSOCIATION, Environmental Aspects of Uranium Mining Web-site (2014). [1]
- ↑ NATIONAL RESEARCH COUNCIL, Uranium Mining in Virginia. Scientific, Technical, Environmental, Human Health and Safety, and Regulatory Aspects of Uranium Mining and Processing in Virginia. US National Academies Press, Washington (2011). [2]
- ↑ NUCLEAR REGULATORY COMMISSION, Standard Review Plan for the In-Situ Leach Uranium Extraction License Application, NUREG-1569. US NRC, Washington (2003).
- ↑ INTERNATIONAL ATOMIC ENERGY AGENCY, Treatment of Liquid Effluent from Uranium Mines and Mills, IAEA-TECDOC-1419, IAEA, Vienna (2005).
- ↑ INTERNATIONAL ATOMIC ENERGY AGENCY, Occupational Radiation Protection, Safety Guide, IAEA Safety Standards No. GSG-7, IAEA, Vienna (2018).
- ↑ INTERNATIONAL ATOMIC ENERGY AGENCY, Monitoring and Surveillance of Residues from the Mining and Milling of Uranium and Thorium, Safety Reports Series No. 27, IAEA, Vienna (2003).
- ↑ INTERNATIONAL ATOMIC ENERGY AGENCY, Guidebook on Good Practice in the Management of Uranium Mining and Mill Operations and the Preparation for their Closure, IAEA-TECDOC-1059, IAEA, Vienna (1998).
- ↑ INTERNATIONAL ATOMIC ENERGY AGENCY, Innovations in Uranium Exploration, Mining and Processing Techniques, and New Exploration Target Areas, IAEA-TECDOC-868, IAEA, Vienna (1996).
- ↑ OECD/NUCLEAR ENERGY AGENCY (NEA), The Safety of the Nuclear Fuel Cycle, Third Edition, NEA No.3588, OECD/NEA, Paris (2005).
- ↑ INTERNATIONAL ATOMIC ENERGY AGENCY, Disposal of Radioactive Waste, IAEA Safety Standards, Specific Safety Requirements No. SSR-5, IAEA, Vienna (2011).
- ↑ INTERNATIONAL ATOMIC ENERCY AGENCY, Establishment of Uranium Mining and Processing Operations in the Context of Sustainable Development, IAEA Nuclear Energy Series Report No. NF-T-1.1, IAEA, Vienna (2009).
- ↑ INTERNATIONAL ATOMIC ENERCY AGENCY, Exposure of the Public from Large Deposits of Mineral Residues, IAEA-TECDOC-1660, IAEA, Vienna (2011).
- ↑ INTERNATIONAL ATOMIC ENERCY AGENCY, The Uranium Mining Remediation Exchange Group (UMREG), Selected Papers 1995-2005, STI/PUB/1524, IAEA, Vienna (2011).
- ↑ INTERNATIONAL ATOMIC ENERGY AGENCY, Best Practice in Environmental Management of Uranium Mining, Nuclear Energy Series NF-T-1.2, IAEA, Vienna (2010).
- ↑ VAN GOSEN, B.S., TULSIDAS, H., Thorium as a Nuclear Fuel, Ch 10 In Hore-Lacy, I. (Ed.), Uranium for Nuclear Power: Resources, Mining and Transformation to Fuel. Woodhead Publishing, Cambridge (2016)
- ↑ ATOMIC ENERGY REGULATORY BOARD, Management of Radioactive Waste from Mining and Milling of Uranium and Thorium, AERB Safety Guide No. AERB/NF/SG/RW-5. AERB, Mumbai, India (2007).[3]